Staff responsible for managing your in-house clinic pharmacy have to deal not only with patients and their prescriptions but also with related documents pertaining to invoices, insurance, purchase orders, expired stock and so on. More often than not, an In-House Pharmacy whose basis of an establishment is offering 1-stop shop convenience to Patients ends up becoming a source of a great deal of pain. Hassled staff- no matter how many hours they put in, find themselves unable to answer the basics of how much stock they have, how much is due to expire shortly, and what is the variance between sale value and stock value. The todos keep getting piled up, till a point comes, where Staff just give up trying to be efficient, letting things be as they are and complacency sets in. All of these issues can be addressed with ease by putting in place an effective In-House Pharmacy Management Software.
The word “in-house” is key here, as just any pharmacy management software will not do. You need a system that is,
- Linked to your Scheduler – so that you know the details of who is purchasing the Rx
- Linked to your EMR – so that you have access to the E-Prescriptions being prescribed by your Clinic’s Practitioner
- Linked to the Insurance Agreements your Clinic has entered into and Membership plans it has issued – so you know the discounted pricing you need to apply on the Rx being purchased and more.
Now that we have touched upon, why is “in-house”, interlinked, and fully integrated pharmacy, the key to the Pharmacy Management System selection process, let us review the 8 must-have features of an In-House Pharmacy Management Software.
1. Support for Key Fields
Entering a new Inventory Item in most Pharmacy Management Systems is either too basic or quite lengthy and irrelevant. It is important to strike a balance between simplicity and usefulness. I will share with you the key fields your In-House Pharmacy Management software absolutely needs to support.
The very basic details about an inventory include Inventory name, Category, and SKU Code.
It should also have support for putting in information about Quantity on Hand (QOH), Re-Order Level and the Unit Buying and Unit Selling Price.
Apart from these basic details, there are a few other details which prove to be very significant when it comes to managing your pharmacy. Here is a list.
(a) Pack Name: This tells you about package details of an inventory. For example, Crocin comes in strips. So the pack name will be ‘Strip’. Similarly, Grilinctus comes in a bottle. In such a case the pack name will be ‘Bottle’.
(b) Pack Dispensing Unit and Pack Size: You have seen that Crocin comes in strips. Now, you should be able to put in details of how it is supposed to be dispensed, that is, whether it would be dispensed in units or a strip as a whole. In case it is to be dispensed in units, it is critical to define the number of units per pack. For example, one strip of Crocin has 10 tablets where ‘Tablet’ is basically the unit name.
(c) Generics: Putting in the generic details of an inventory can prove to be very helpful as it can make brand substitution possible. Let us consider one scenario to understand this. Your Pharmacy keeps two paracetamols- Crocin and Calpol. You have prescribed your patient one strip of Calpol and mentioned that brand substitution is allowed. In case your inventory runs out of stock of Calpol, your pharmacist can make sure that the patient does not have to return empty-handed by dispensing the other available paracetamol (generic name), Crocin to the patient.
(d) Coding: Coding for Rx has already caught on in some countries. RXNORM is the standard popular in the US. Singapore too has implemented its own coding scheme for drugs, SDD. Coding basically results in each Rx brand/generic being associated with a unique code through which prescriptions from across medical facilities can be digitally collated and understood.
(e) Mode of Dispensing: There can be multiple ways of dispensing inventories which vary from clinic to clinic. The mode in which inventories are dispensed can be FIFO, LIFO, Expiry Date or Manual. You will learn more about how this dispensing works as I take you through the next point.
2. Support For Batching
It is quite common practice for clinics to maintain Inventory in batches. When an inventory is maintained in batches, there has to be a mechanism for dispensing too. This method of dispensing is called into use when you decide to bill stock items. At that point in time, the software needs to select the inventory on your behalf. It makes this selection based on the dispensing method setup for that particular item of Inventory. Dispensing can be done in one of the various ways- i.e. FIFO, LIFO, Expiry Date and Manual. Let’s go over each approach.
1. FIFO – In this case, inventory belonging to an older batch will be dispensed first. For example, if there are 2 batches of this stock, one that came in Jan, and the other in Feb, the batch from Jan will be selected by the software for dispensing if the dispensing method is set as FIFO.
2. LIFO – Setting this will dispense stocks from the latest batch first. Going by the above example, the batch in Feb will be picked up first.
3. Expiry – If your preference is set to dispense as per expiry date, the inventory expiring first will be picked up first. For example, if there are 2 batches of this stock- one that expires in Jan, the other in Feb, the batch from Jan will be picked up for auto-dispensing at the time of billing.
4. Manual – At the time of Billing the pharmacist will manually select the batch of the Rx. This approach allows for maximum control but no automation is possible as everything is manual.
Do make sure that your Pharmacy Management System supports each of the batching methods, and that it has the option to vary the dispensing mode for each item of the inventory.
3. Support for Bar-code Scanning
Earlier in this article, I mentioned SKU Code as one of the basic details that you should be able to store in the system. Here you will see how this proves to be useful in Pharmacy Management.
SKU stands for Stock Keeping Unit and is basically a unique ID specific to an inventory so it can be easily identified when searched for. When you put in the SKU, it generates a machine-readable code that is unique compared to all the other inventories that you have in your pharmacy. This barcode is generally put on the Inventory’s Packaging, or an Inventory item may already come packaged with a barcode given to it from the manufacturer. This feature also helps you in billing patients easily as you need not type in the item details, just scan the barcode on the inventory package with the help of a barcode scanner.
As soon as the item is scanned, the cashier is provided with all the details specific to the product making it easy to bill you instead of manually putting in all the details one by one into the system. Make sure to go for a system that has this feature enabled.
4. Alert on Inventory Levels
For this feature to be functional, it is important to store the details of QOH and Re-Order Level as part of the basic details of the inventory. QOH refers to the current quantity of your inventory and keeps on decreasing as your pharmacist dispenses. Re-Order Level refers to the quantity threshold at which your software should alert you to place a new order for stock.
Your Pharmacy Management Software should have the capability to alert you via email/SMS or both, when this threshold is breached so that you place an order in time and never run out of stock, as that is revenue lost.
5. Stock Intake and Stock Transfer
- Clinic to Vendor
When you are out of stock of your inventory, you would call for your vendor to supply the same. Your provider should be able to support this. You should be able to raise a purchase order for the vendor and also track the same. When you intake stock, you should be able to put in details of each inventory being bought e.g. quantity purchased, pack size, free packs you got, buying and selling price, applicable taxes and so on. Once you have received the stock, the system should auto-update the quantities of the inventory received to reflect the purchase. Most large clinics usually put in a 2nd level check too, which requires incoming stock to be authorised by yet another person, so that deliveries are cross verified. The system should also raise a debit note on the vendor, in case the inventory quantity supplied is less than ordered, or a credit note, in case the extra stock has been supplied.
- Clinic to Clinic
In case you are having a clinic chain, there can be situations where you transfer stock internally. The flow to this would be similar to the stock intake from the vendor except that in this case, the supplying clinic should have its inventory reduced automatically, while the receiving clinic should have its quantity increased.
6. Stock Take
Stock-taking or “inventory checking” is the physical verification of the quantities and condition of items held in an inventory or warehouse. It is a manual process where the physical quantity of an item, currently on the shelf, is counted and compared with the QOH in the software. Discrepancies between your manual stock count and your electronic records allow you to pick up on a range of issues and put processes into place to ensure better stock control and management. Given its usefulness, your In-House Pharmacy Management Software should definitely have the support for Stock-Takes.
7. Reporting
At the end of the month, you should be able to tally the revenues generated by the movement of stocks. You should get details of the sale of each unit of an inventory or even if some has been disposed off or damaged, to ensure that you don’t end up losing out even a penny without it being accounted for.
8. Data Loading
As and when you plan to get your pharmacy live, you will definitely be having loads of data to put into the system owing to the large number of items that you will maintain in the pharmacy. Humanly, it is never possible to put in the details of each inventory one by one, no matter how many resources you put behind it. Even if you plan to do it, it will not guarantee you that the data entered into the system is free of any errors. So your software should have the facility to load in all the data from an excel/CSV file to make your startup pains go away.
All of these features combined will surely help you take your pharmacy to a whole new level. So keep this checklist handy and make sure the system you choose can answer YES to all of the above.
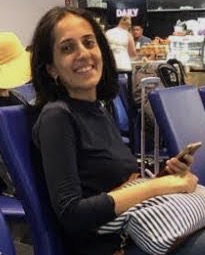
I love writing, especially about health tech :). Feel free to reach out to me with your comments and feedback at rachanas@emrmagazine.com